Thermoplastic composite battery trays are becoming a key technology in the new energy vehicle sector. Such trays incorporate many of the advantages of thermoplastic materials, including light weight, superior strength, corrosion resistance, design flexibility, and excellent mechanical properties. These properties are critical to ensuring the durability and reliability of battery trays. In addition, the cooling system in a thermoplastic battery pack plays a vital role in maintaining the performance of the battery, extending its life, and ensuring safe operation. An effective thermal management system ensures that the battery is maintained within the desired temperature range under all operating conditions, thereby increasing battery efficiency and safety.
As an enabling technology for fast charging, Kautex demonstrates the implementation of two-phase immersion cooling, where the traction cell is used as an evaporator in the cooling process. Two-phase immersion cooling achieves an extremely high heat transfer rate of 3400 W/m^2*K while maximizing temperature uniformity within the battery pack at the optimal battery operating temperature. As a result, the battery thermal management system can safely and permanently manage thermal loads at charging rates above 6C. The cooling performance of two-phase immersion cooling can also successfully inhibit heat propagation within the thermoplastic composite battery shell, whereas the introduced two-phase immersion cooling dissipates heat into the environment up to 30°C. The thermal cycle is reversible, allowing efficient heating of the battery in cold ambient conditions. The implementation of flow boiling heat transfer ensures constant high heat transfer without vapor bubble collapse and subsequent cavitation damage.
Figure 1 Thermoplastic component housing with two-phase cooling systemIn Kautex’s direct two-phase immersion cooling concept, the fluid is in direct contact with the battery cells inside the battery housing, which is equivalent to an evaporator in a refrigerant cycle. Cell immersion maximizes the use of the cell surface area for heat transfer, while constant evaporation of the fluid, i.e. phase change, ensures maximum temperature uniformity. The schematic is shown in Figure 2.
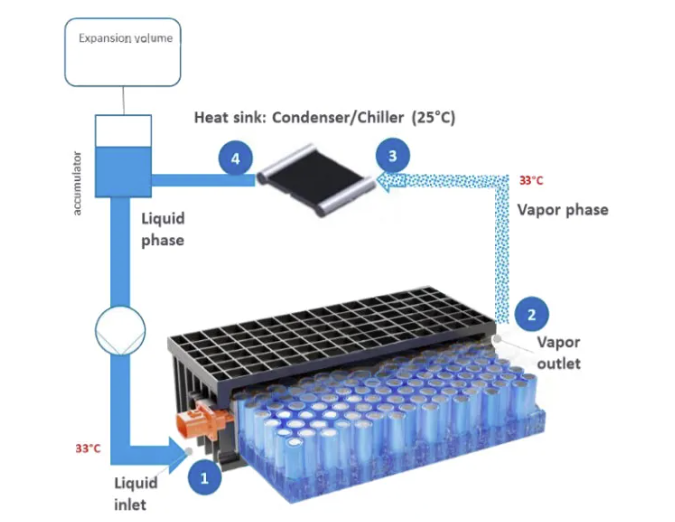
Fig. 2 Principle of operation of two-phase immersion cooling
The idea of integrating all the necessary components for fluid distribution directly into a thermoplastic, non-conductive battery shell promises to be a sustainable approach. When the battery shell and the battery tray are made of the same material, they can be welded together for structural stability while eliminating the need for encapsulation materials and simplifying the recycling process.
Studies have shown that a two-phase immersion cooling method using SF33 coolant demonstrates superior heat dissipation capabilities in transferring battery heat. This system maintained battery temperatures in the 34-35°C range under all test conditions, demonstrating excellent temperature uniformity. coolants such as SF33 are compatible with most metals, plastics, and elastomers, and will not damage thermoplastic battery case materials.
Fig. 3 Battery pack heat transfer measurement experiment [1]
In addition, the experimental study compared different cooling strategies such as natural convection, forced convection, and liquid cooling with SF33 coolant, and the results showed that the two-phase immersion cooling system was very effective in maintaining the battery cell temperature.
Overall, the two-phase immersion cooling system provides an efficient and uniform battery cooling solution for electric vehicles and other applications requiring energy storage, which helps to improve battery durability and safety.
Post time: Oct-14-2024